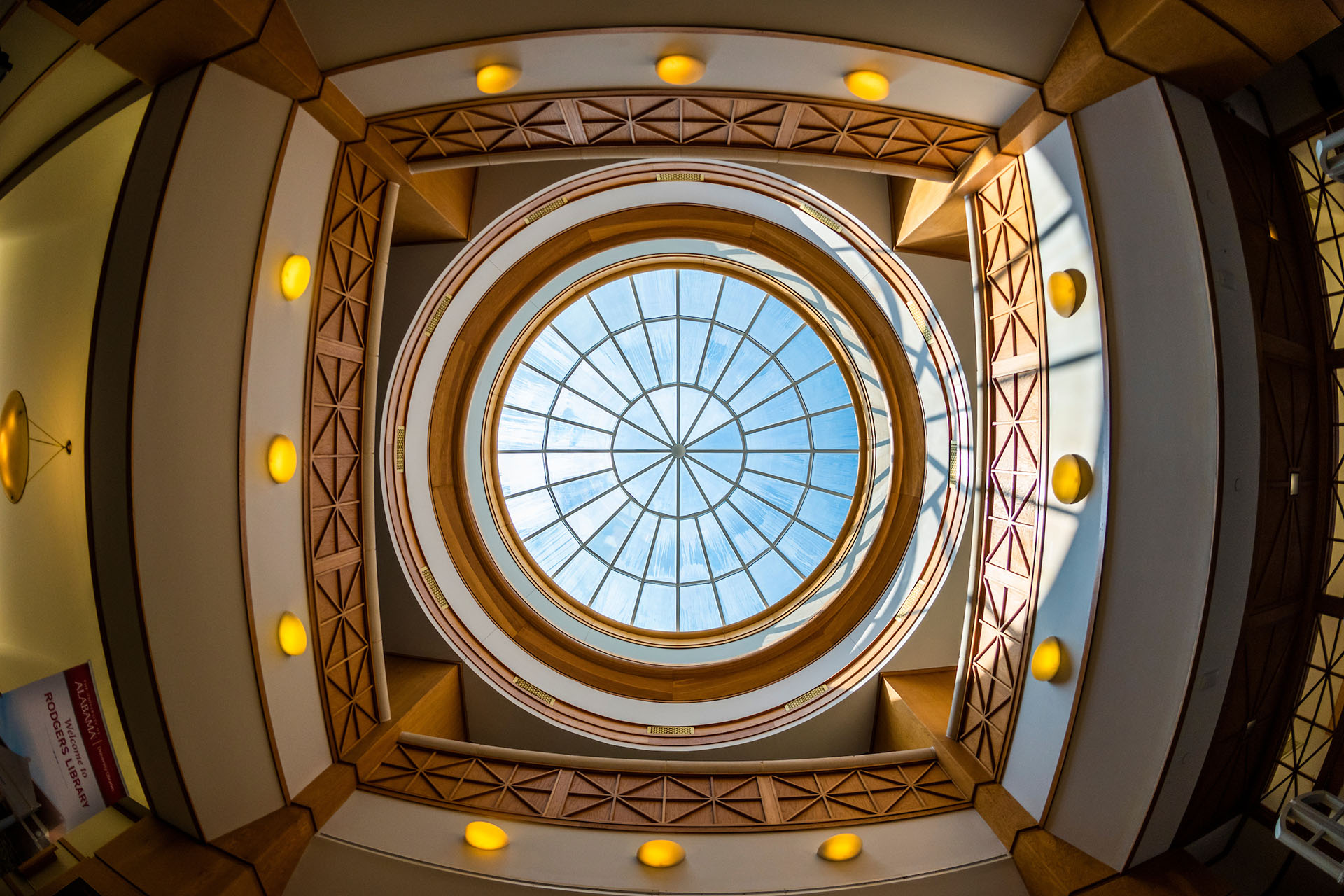
Research
Our faculty and students conduct research in four core areas: aeronautics, astronautics, fluid mechanics, and solid mechanics and structures. Excellent facilities as well as graduate and undergraduate assistantships support these areas.
News
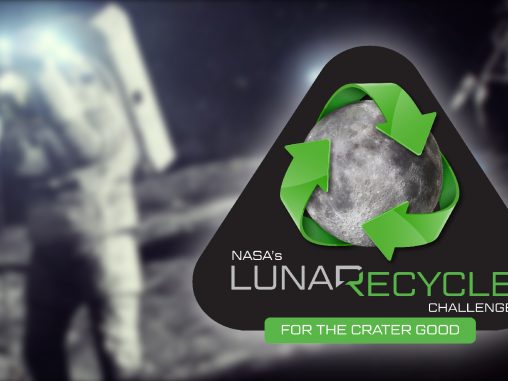
Innovators from 9 U.S. States, 4 Countries Win Phase 1 of NASA’s LunaRecycle Challenge
LunaRecycle, a NASA Centennial Challenge, launched in September 2024 to crowdsource solutions for recycling non-metabolic materials on space exploration missions. The competition focuses on the design, development and demonstration of...

Alabama Astrobotics Team Digs into Success at NASA’s Lunabotics Challenge
The Alabama Astrobotics Team recently returned from NASA’s 2025 Lunabotics Challenge with national recognition for its innovative approach to lunar robotics and systems engineering. Hosted annually at NASA’s Kennedy Space...
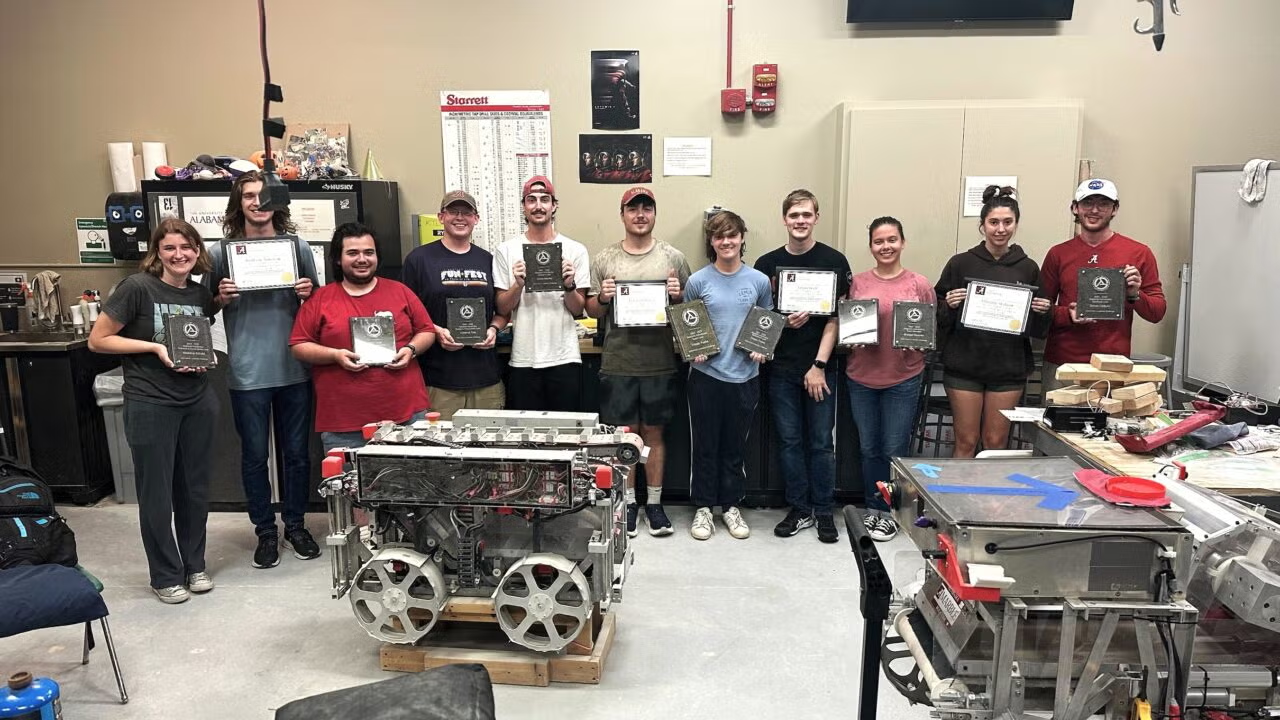
UA Astrobotics Finishes Strong in Lunar Robotics Competition
With less than a week before the final event of the 2025 NASA Lunabotics Challenge, members of The University of Alabama Astrobotics team were working in shifts to fine-tune their...

Research Opportunities
For more information regarding undergraduate research opportunities contact Dr. Semih Olcmen, Undergraduate Program Coordinator, and for graduate research opportunities contact Dr. Paul Hubner, Graduate Program Coordinator.
Laboratories
Advanced Materials Behavior Laboratory (Dr. Mark Barkey) – This laboratory is a research and instructional facility for the study of solid materials under monotonic, cyclic and constant load conditions. Three MTS machines, two Instron machines, two creep machines and one drop-weight impact machine are the principal load frames. A microcomputer is used for data acquisition and control in this facility.
Aerospace Structures Laboratory (Dr. Anwarul Haque) – This laboratory is equipped for the characterization of flight vehicle structural components under tension, compression, bending and cyclic loading. A servohydraulic testing machine equipped with a high temperature and cryogenic environmental chamber is available. Strain gage mounting devices and multi-channel digital strain indicators are extensively used for strain monitoring and transducer design. A machine shop and composite materials laboratory facilitate specimen and structural component fabrication.
Astrodynamics and Space Research Laboratory (Dr. Rohan Sood)
Composite Material Laboratory (Dr. Anwarul Haque, Dr. Samit Roy) – This laboratory includes facilities for manufacturing, characterization and modeling of advanced composite materials. A compression molding hot press, filament winder, pultrusion equipment, extruder and resin infusion vacuum pumps are available for manufacturing thermoset, thermoplastic and nanocomposites film, plates and structural components. Dispersion equipment such as ultrasonic bath, tip sonication and mechanical high shear mixer are also available for processing polymer nanocomposites. A MTS servohydraulic testing machine and Hopkinson Bar test equipment facilitate characterization of composite materials under static, cyclic and high strain rate loading. Fracture analysis and microstructural studies are carried out using available optical, scanning and transmission electron microscopes (central facility). The laboratory is equipped with a number of computational workstations for analytical and numerical simulations. ABAQUS, NASTRAN, DYNA 3D, ALGOR finite element codes, and a Hypermesh geometric model generator are available in workstations for finite element analysis. An in-house FEA code for predicting long term environmental durability of polymer and polymer composites is also available.
Computational Fluid Dynamics Laboratory (Dr. Muhammad Ali Rob Sharif)
Experimental Stress Analysis Laboratory (Dr. Mark Barkey) – This laboratory is used for the experimental measurement of force, strain, displacement, and acceleration. Equipment for both static and dynamic measurement is available, including oscilloscopes, accelerometers, load cells, LVDTs and a variety of strain-conditioning and measuring devices. Also available is equipment for photoelastic analysis, including a transmission polariscope, a reflective polariscope, a stress-freezing oven and associated tools for model preparation.
High-Speed Fluid Mechanics Laboratory and Supersonic Tunnel (Dr. Semih Olcmen) – The large supersonic wind tunnel is a 6″ X 6″ blow down facility with a Mach number range of 1.5 to 3.5. The system includes a 1,000 ft3 high-pressure air storage facility, two compressors and aftercooling-airdrying accessories. Plenum chamber pressure is controlled using three pressure transducers together with a fuzzy logic controller. Nine pressure transducers and accompanying hardware and software are available for total or static pressure measurements. The tunnel is equipped with a four-component force-balance system and accompanying eight-component strain-gage data acquisition system. A Schlieren/shadowgraph optical system using a Strobotac light source is also present for flow visualization.
The high-speed fluid mechanics laboratory also includes a small-scale high Reynolds number (20-150 x 106/m), variable Mach (0.25 through 4.0) wind tunnel with a 4″ X 4″ test section. This facility was constructed for basic fluid mechanics research. The tunnel is used in high-speed boundary layer, missile aerodynamics, reaction control jet and flow control studies.
Impact and Penetration Mechanics Laboratory (Dr. Mark Barkey) – The Impact and Penetrations Laboratory investigates the performance of projectile and target materials in the extreme environment of a penetration test. Projectiles are launched in a variety of calibers as large as 0.500” and as small as 0.167”. Targets used have been armor, concrete, sand, soil and glass. Impact velocities are as high as 1000 m/s. All the launchers are smooth bore powder guns which were designed and built at the University. The laboratory also includes a Taylor Cylinder Test facility which accommodates all of the aforementioned specimen calibers, and data from the tests allows us to estimate the properties of ductile materials at strain rates as high as 105/sec.
Jet Propulsion Stand (Dr. Semih Olcmen) – The propulsion laboratory is centered on a small turbojet engine and its accompanying test stand. The turbojet engine generates a maximum of 20 pounds of thrust, runs on kerosene, diesel, or standard jet engine fuels, and weighs less than 12 pounds. Although smallscale, the turbojet engine operates just like any gas turbine engine. It has an inlet, single-stage radial compressor, reverse flow combustion chamber, axial turbine and an exhaust nozzle. The engine, mounted inside a test stand, is fitted with thermocouples, pressure taps and strain gages allowing all aspects of the engine to be monitored in real-time. The test stand has been modified to be used as a test bed for rocket and air-breathing propulsion research. Several artificial intelligence algorithms including, PID, fuzzy logic and neural networks have been applied to the engine under various research projects.
W.D. Jordan Laboratory (Dr. Mark Barkey) – This laboratory serves as the primary facility for the AEM 251 Mechanics of Materials Laboratory. The facility contains four universal testing machines for the performance of tension, compression, bending and shears tests of specimens and structures; two torsion testing machines; an impact machine; three hardness testing machines; a microcomputer system for data collection, manipulation and graphic output; and other mechanical testing equipment.
Laser Doppler Velocimetry Laboratory (Dr. Semih Olcmen) – The laser Doppler velocimetry lab includes a 15 Watt Ar-Ion laser, a frequency domain processor, several Bragg cells and photomultipler tubes for three-component velocity measurements. The lab includes a miniature two component probe, a miniature three component probe and a three-component homemade fiber-optic LDV probe for simultaneous velocity measurements in flow fields ranging from low speed to high speed applications. Current research includes velocity and turbulence measurements inside the engine of a commercial car engine as well as high and low speed jet flows.
Low-speed Wind Tunnels (Dr. Semih Olcmen, Dr. Paul Hubner) – The department has two low-speed wind tunnels that can operate in three different configurations. The newest tunnel is the boundary layer tunnel. This open circuit tunnel has an 8.5:1 contraction that leads to a 16 ft long test section with cross-sectional dimensions of 12 in by 36 in. The maximum speed is over 45 m/s and the latter half the test section includes a variable positioning ceiling to create user-defined adverse pressure gradients. In addition to the boundary-layer configuration, the tunnel was designed with a second interchangeable contraction that leads to a more conventional 6 ft long test section with 30 in by 30 in cross-sectional dimensions. The speed range is 1 m/s to 20 m/s for low Re and MAV testing. Both test section configurations have 360 degree optical access. The third tunnel is a conventional, closed-circuit wind tunnel designed and built in the 1930s but still in use today. The maximum velocity is approximately 100 mph. The contraction ratio is 4:1, leading to a 44 in by 29 in test section. The tunnels are equipped with state-of-the-art equipment including a V3V three-component velocity measurement system, hotwire anemometry system, digital pressure scanners and sensors, multi-channel DAQ devices for analog voltage input and strain gage signal conditioning suitable for force-balance measurements, PC-controlled traversing systems as well as many other tools.
Luminescent Imaging Laboratory (Dr. Paul Hubner) – This research laboratory is used to develop, study and apply molecular luminescent techniques used in the field of experimental fluid and solid mechanics. Applications of these techniques are widely useful to the aerospace and automotive communities as these methods bridge physical testing and analytical modeling in a variety of areas. Examples include load and heating predictions on aircraft, evaluation of fluid-structure interactions, validation of computational methods, nondestructive detection of potential failure locations on mechanical components and inverse-method techniques to determine load and boundary conditions. The facility includes digital imaging equipment, a suite of supporting optics and excitation lamps, PC-based data acquisition and conditioning workstations, a coordinate measurement machine, optical work benches, electric and pneumatic linear actuators and a specimen preparation area including a six foot bypass fume hood.
Senior Design Laboratory (Dr. James P. Hubner) – This 500-square-foot lab is dedicated for the undergraduates enrolled in Senior Design (AEM 402 and 404).
Structural Durability and Fatigue Performance Group (Dr. Mark Barkey) –
Thermal Pultrusion Laboratory (Dr. Samit Roy) –
Water Tunnel Laboratory (Dr. Amy Lang) – The water tunnel has a 15 inch wide by 30 inch tall by 9 foot long test section and is capable of speeds up to 1 ft/s. This tunnel has been designed to run at very low turbulence levels (0.5% or less) and also has a two dye injection system. The tunnel is currently outfitted for obtaining boundary layer measurements over a flat plate. The laboratory also includes a Time Resolved Digital Particle Image Velocimetry (TR-DPIV) system capable of capturing images of the flow at 1000 fps. This system acquires velocity data within a two-dimensional plane by imaging and tracking particles that have been illuminated in the flow through the use of a laser sheet.
SEMINARS
Department of Aerospace Engineering and Mechanics Seminar Series
Time: tbd
Location: tbd
Theme | Date | Speaker | University/Institute |
---|
